OK, as you recall, the back plates were thermally modified, but the sides were not. The reason for this is that thermally modified sides are very difficult to bend, thus, a workaround. The sides will be bent first, and then thermally modified. It is actually a very simple process.
The sides can be bent using whatever method/process works for you. The important part is that you get a good bend with no springback. The other thing is that you will need to end up with the bent sides wrapped in a layer of kraft, or similar paper, and then aluminum foil. I will show my process and you can adapt accordingly to your process.
I use a thermostatically controlled heating blanket and a bending form with cauls to clamp the sides. I usually set the temperature around 325 F. I have better luck bending if I dip or soak the sides in hot water for a few minutes on softer woods to up to a half hour with dense rosewood. Do what works for you...it will not matter.
So, after I have soaked one of the mahogany sides, I wrap in white Kraft paper (brown will work, too)
Then aluminum foil
Here it is ready for the bender
I did not photo the actual bending operation, like I said, do what works for you. I bend at 325 F and have found that a second heating cycle of 5 or 6 minutes at 350 F will totally set the bend and prevent springback.
Here are both sides, bent
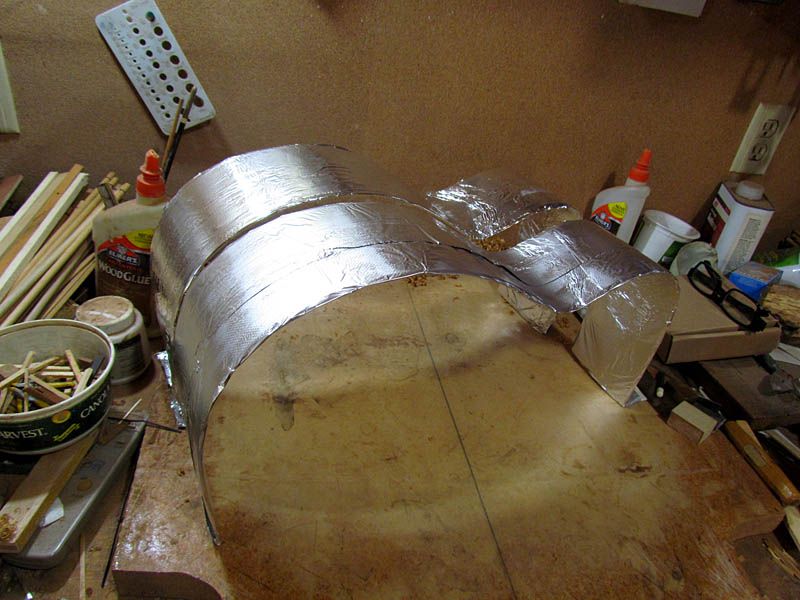
Notice, I have left them wrapped. Now, if you bend on a hot pipe or otherwise do not wrap sides for bending, just wrap them afterwards. Tip: fold the paper and aluminum foil down the center and insert the bent sides from the side like putting into an envelope.
So on to the kitchen oven. You will be cooking these at 380 F (way cooler than a pizza). Set the oven temperature and put in the sides. Then turn it on
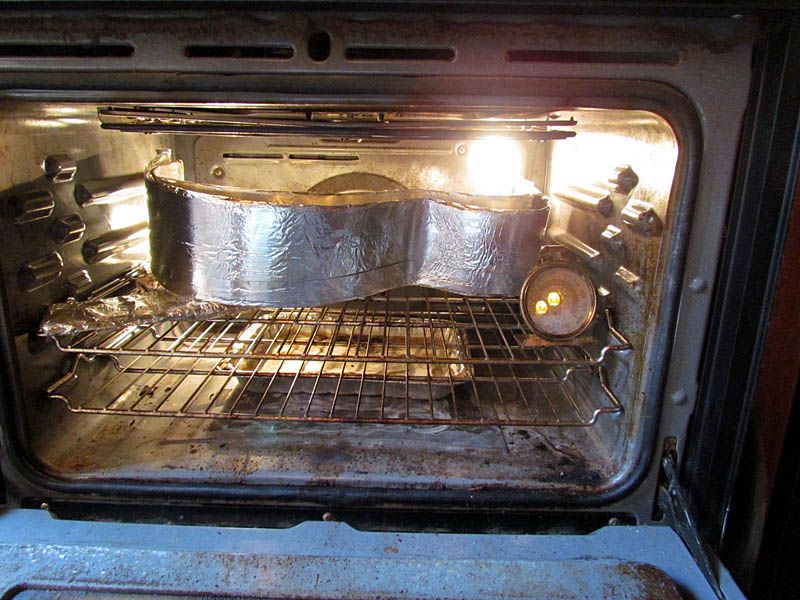
I don't trust the temp setting, so I also use an oven thermometer. (notice the aluminum foil wrapped packets under the sides...bracewood being cooked at the same time)
Once the temperature is up to the 380 F let the sides bake for 40 or 50 minutes. Then remove the sides, they are done. Keep in mind that although the Thermowood process goes for around 72 hours, the kiln is only at maximum temperature for an hour or so.
So here is a side done
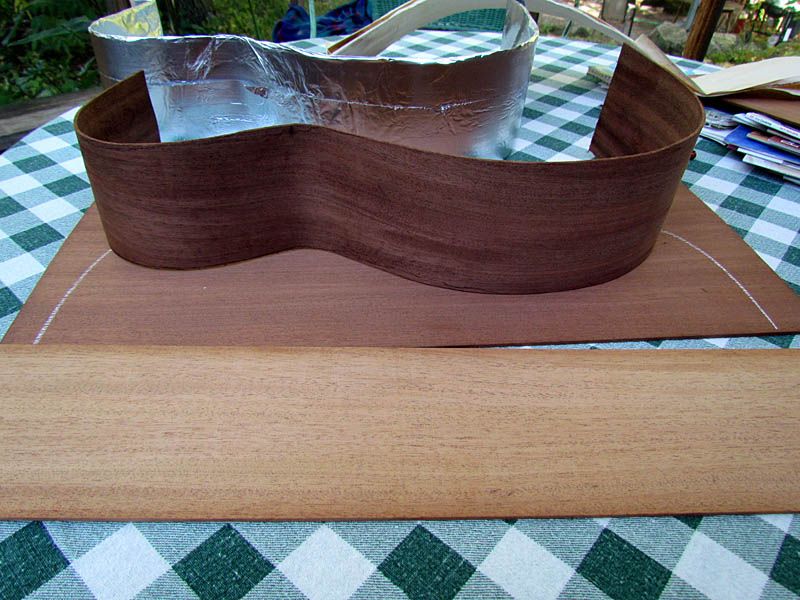
It looks darker than the treated back under it, but that is mostly the light angle plus a small amount of surface darkening that sands off. The piece in the foreground is an untreated side
Another photo
And with the second side, still wrapped in the Kraft paper
That is all there is to it. Questions/comments are welcome.
BTW, I will send a couple of pieces of the white Kraft paper along with the drawing prize.
G